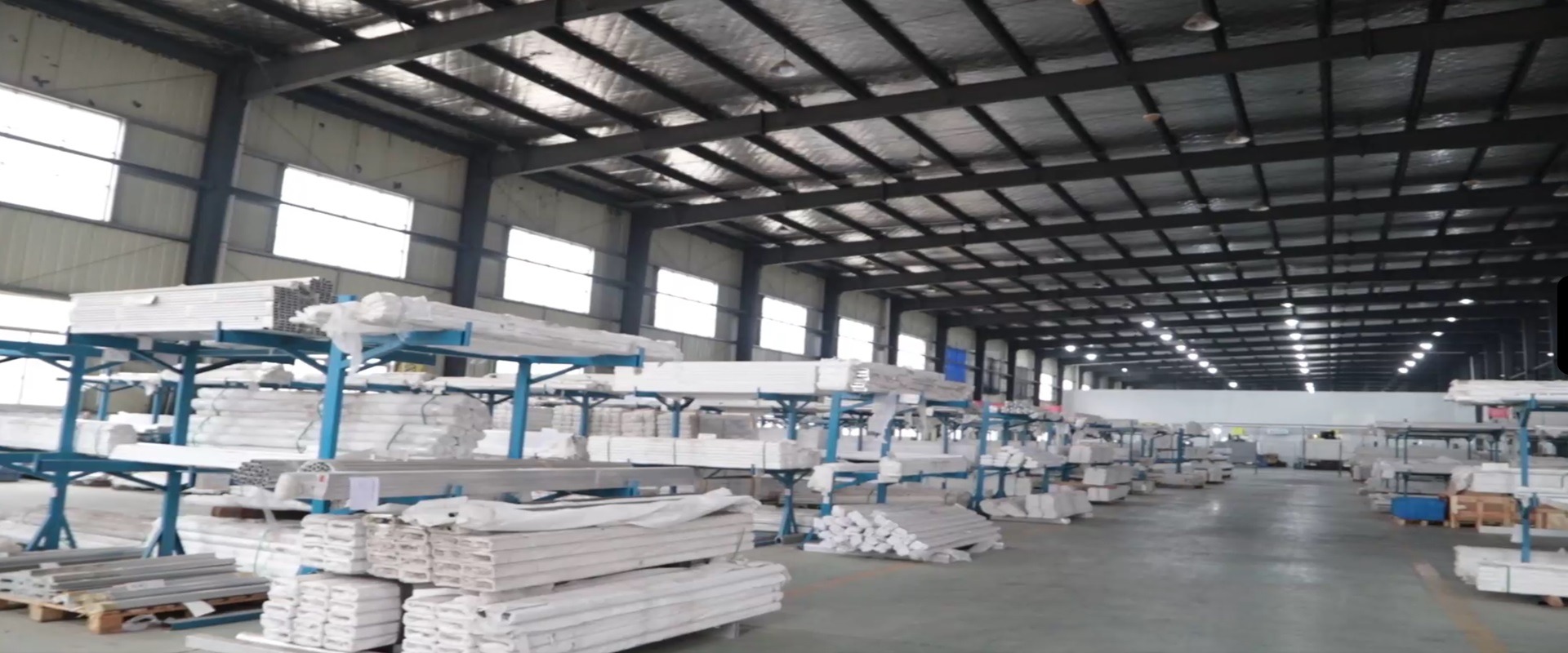
Innovative Production Specialist-CNC Machining Services, Sheet Metal Fabrication, CNC Tube & Pipe Bending Forming Services
About MachiningFabTech
Since 1997, MachiningFabTech has always trying to be one of the leaders in precision manufacturing, offering 20+ years of hands-on experience in delivering high-quality solutions for industries worldwide. We specialize in OEM & ODM manufacturing, providing tailored services such as:
- CNC Machining Parts
- Sheet Metal Fabrication
- CNC Tube & Pipe Bending/Forming
- Stamping Parts
- Plastic Injection Molding
Industries We Serve:
From automotive and aerospace to medical equipment and renewable energy, our solutions power industries that demand precision and reliability, including oil & gas, hydraulic systems, industrial automation, and more.
Why Work With Us?
- One-Stop Expertise: Our full-range facilities handle every step from design to production, streamlining your workflow and reducing costs.
- Proven Quality: Combining advanced technology with strict quality checks, we ensure every part meets global standards.
- Skilled Team: Our dedicated employees, many with over 15 years of experience, are the backbone of our success. Their expertise drives innovation and consistency in every project.
At MachiningFabTech, we believe in building lasting partnerships through transparency, reliability, and exceptional service. Let us turn your ideas into reality.
Contact us today to discuss your next project!
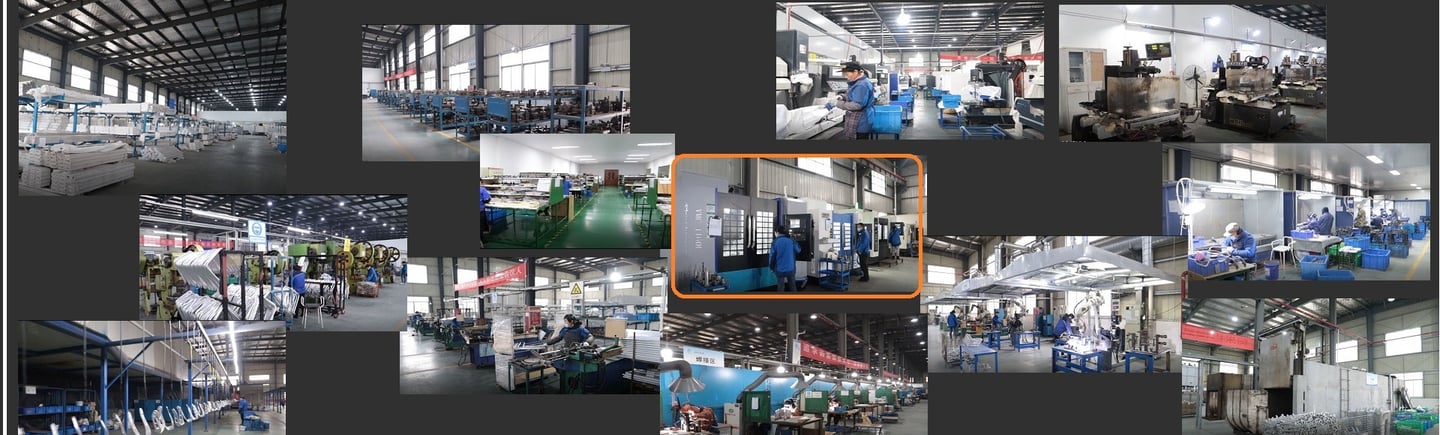
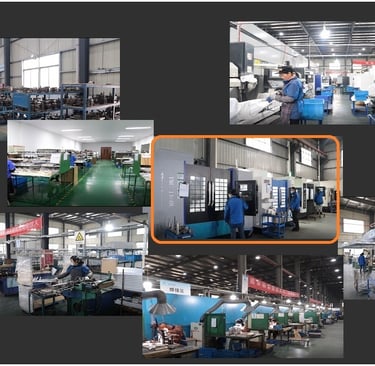
Machiningfabtech Workshops
CNC Machining Services
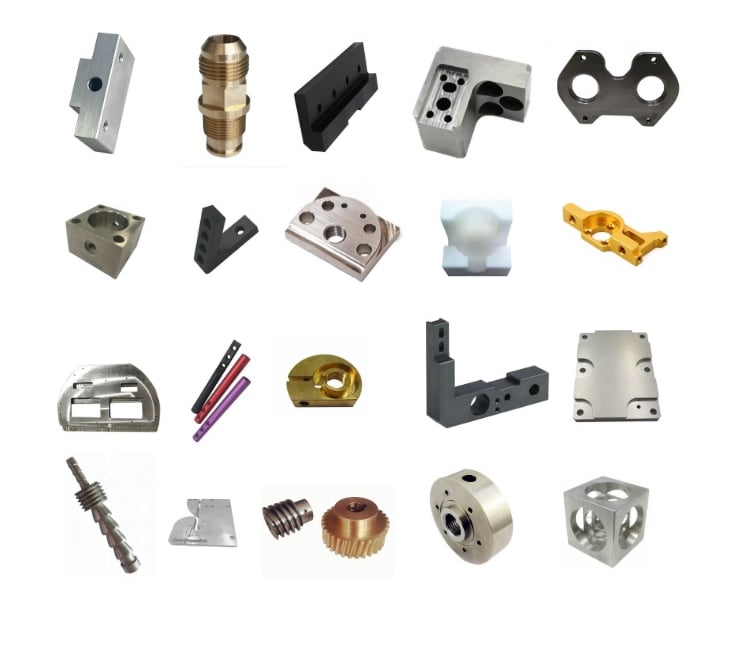
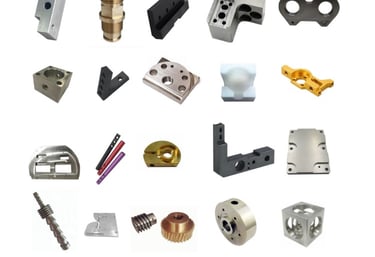
Driving Innovation Through Custom CNC Machining services for R&D
In the field of Research and Development (R&D), the ability to prototype and iterate quickly is essential for driving innovation. At Machiningfabtech, our CNC machining services are designed to support R&D teams with custom, precise machining capabilities. Whether you are developing a new product for the automotive industry or testing components for AI technology, we offer tailored solutions that meet your exact specifications.
Our experienced engineers collaborate closely with R&D departments, offering insights into material selection, machining processes, and design feasibility. This partnership accelerates the development cycle, enabling teams to test and refine concepts rapidly without compromising on quality.
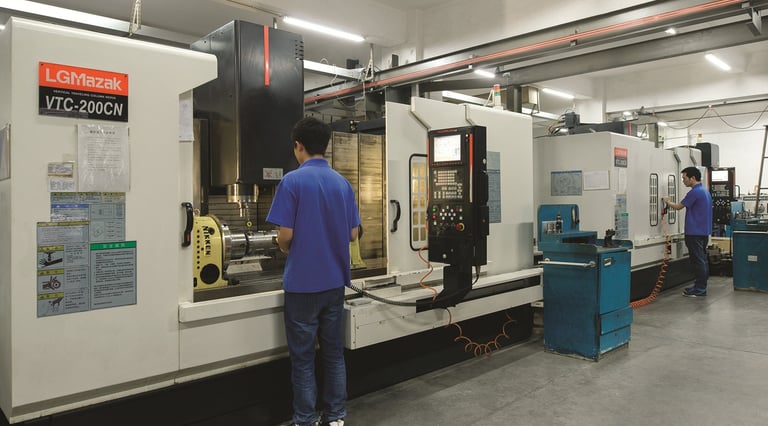

Sheet Metal Fabrication
For R&D engineers, speed is a critical factor in product development. Machiningfabtech offers advanced sheet metal fabrication services that help R&D teams quickly move from concept to prototype. Our ability to fabricate complex designs with tight tolerances ensures that prototypes are not only produced fast but also with the accuracy needed for real-world testing.
Our engineers understand the unique challenges faced in R&D and work closely with your team to ensure that the fabrication process aligns with your development timeline and goals. Whether you are working in the automotive, new energy, medical, or hydraulic sectors, we help bring your ideas to life efficiently.
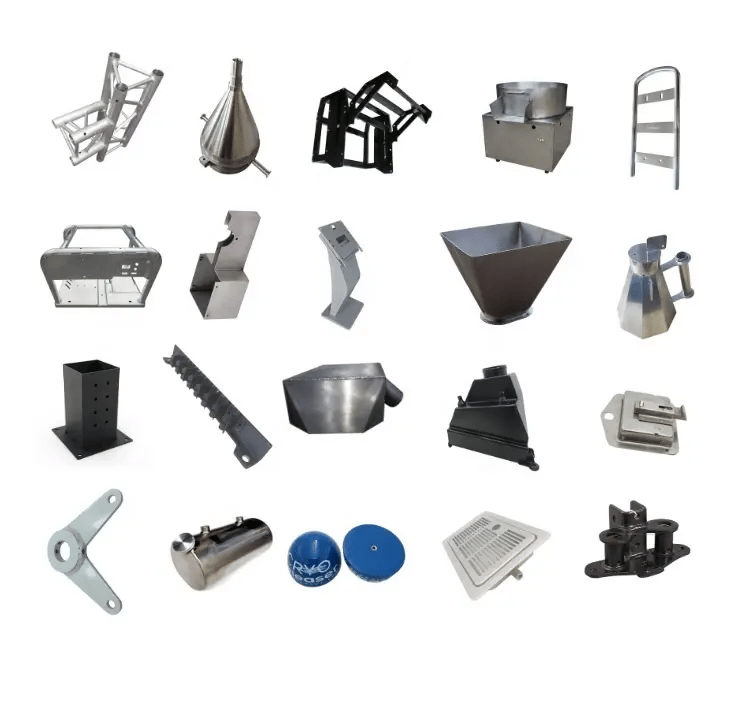
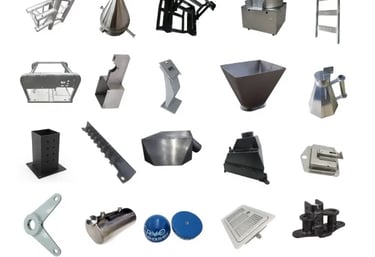
CNC Tube Bending Services
Provide a short summary of your recent projects, highlighting the most important things.Reducing costs in CNC tube bending services is essential for maintaining a competitive edge, especially when handling high-volume production. However, it's vital to maintain quality throughout the process. Here's how to achieve cost efficiency without sacrificing quality:
Improve Production Efficiency
Investing in skilled labor and state-of-the-art machinery can enhance production efficiency. Machines that can automate multiple processes reduce the need for extensive manual intervention, speeding up the production cycle and lowering labor costs.Standardize Components
Wherever possible, using standardized tube components and sizes can reduce customization costs. Standardized parts are often cheaper and more readily available, reducing lead times and costs.
Reduce Material Wastage
Proper planning and design ensure the right amount of material is used, avoiding excess wastage. Accurate measurement and cutting software can help minimize errors and material loss, which directly impacts.Improve Workflow Optimization
Streamlining the production line with lean manufacturing techniques reduces downtime and waste. Efficient workflow optimization ensures that CNC tube bending machines are used to their full potential, maximizing output while minimizing energy and labor costs.Outsource Non-Core Tasks
Consider outsourcing non-core tasks like logistics and finishing services to reliable third-party vendors. This allows your team to focus on core production activities while benefiting from the cost efficiencies of outsourced services.
By implementing these strategies, you can significantly lower costs without compromising on the final product’s quality.
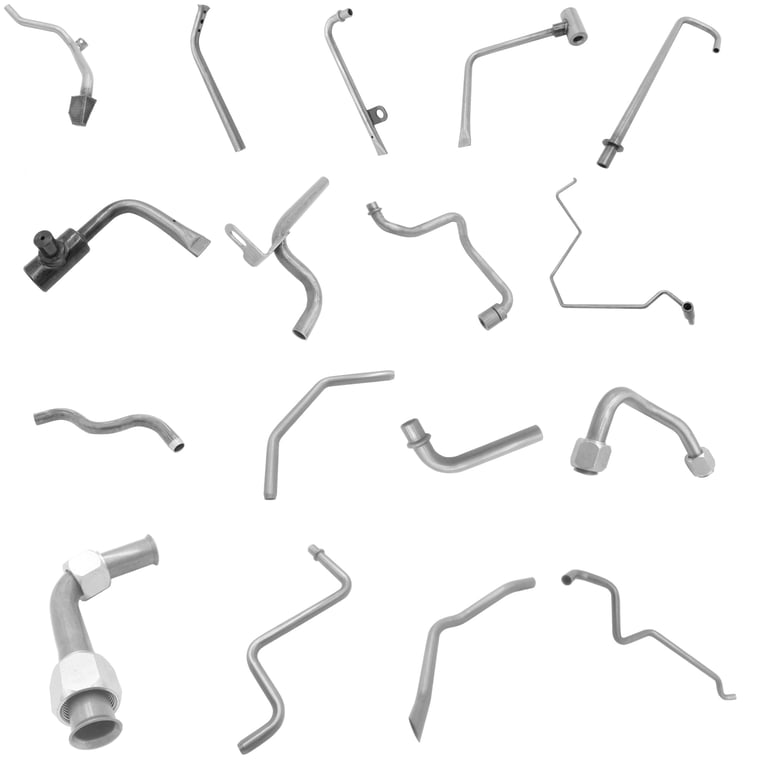
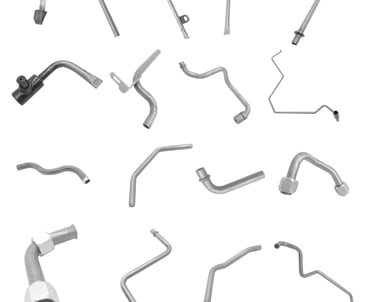
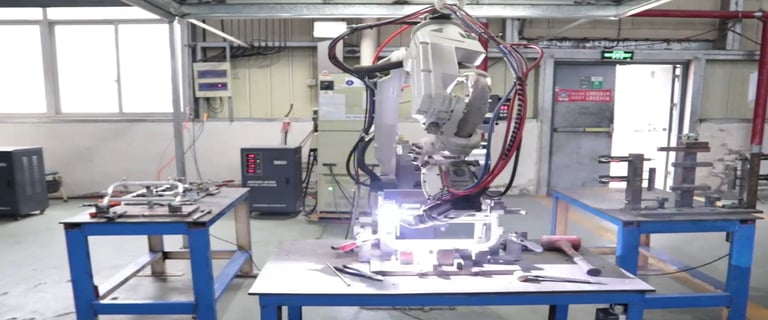
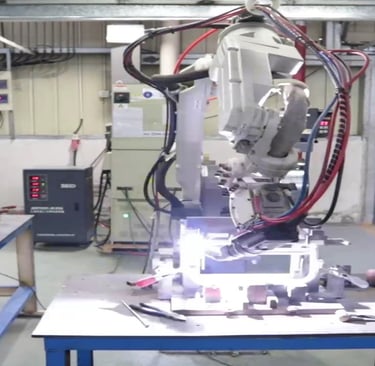
How to Cut Costs in CNC Tube Bending Services While Maintaining Quality
Follow Us
Contact
© 2024. All rights reserved.
Privary Policy
Refund Policy